Directed Energy Deposition
Directed Energy Deposition (DED) is an Additive Manufacturing (AM) process which forms a part or rebuilds a part by depositing material melted by focused thermal energy from a laser, or electron beam. DED is highly precise in its ability to produce complex geometries with near net shape precision.
ES3 developed, qualified, and implemented a knife-edge restoration repair for the TF33 Gas Turbine Engine front and rear compressor spacers; the process was implemented at Tinker AFB. We modified a Trumpf TruLaser Cell 3000 machine to enable the knife edge repair with Ti-6Al-4V, Incoloy 901, 17-22A Steel, and 4340 Steel.
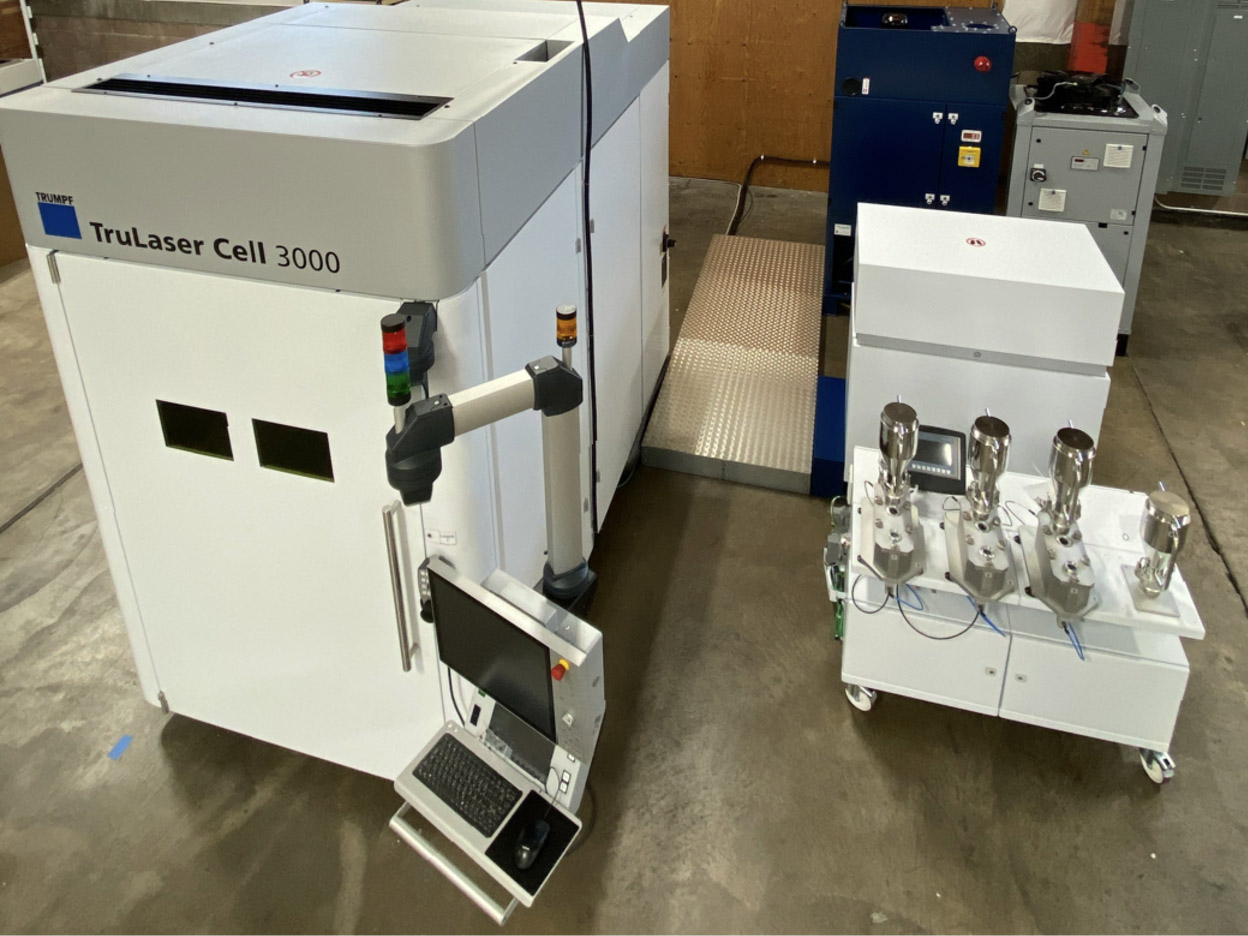
The DED process rebuilding the knife edge seal on the engine compressor spacers.
ES3 also developed, qualified, and implemented a DED flange repair for a gas turbine compressor case; the process was implemented at Tinker AFB. We customized a DMG Mori Lasertec 125 DED Hybrid machine to affect the 410 stainless steel compressor case repair.
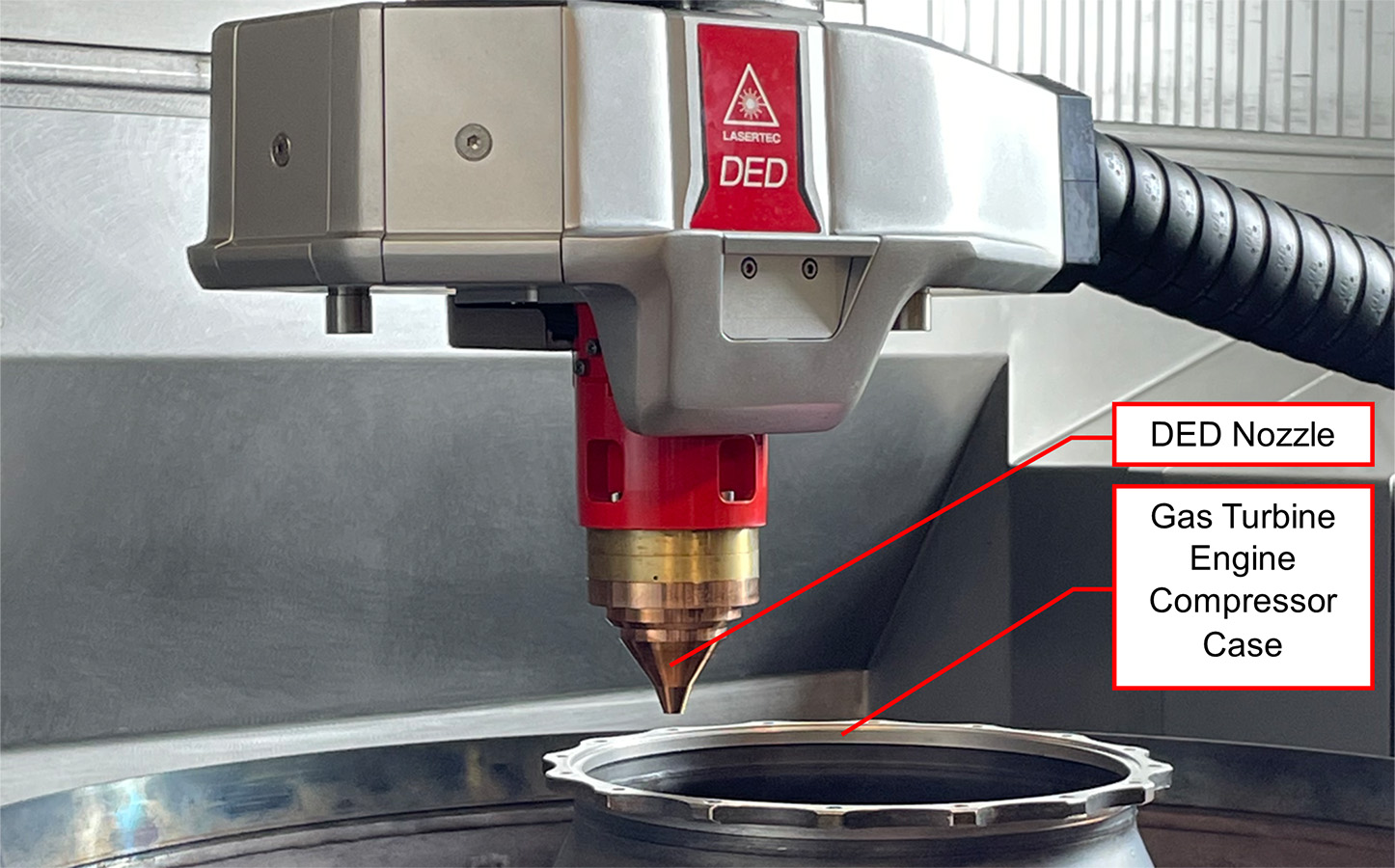
The ES3 system to DED rebuild a gas turbine compressor case.
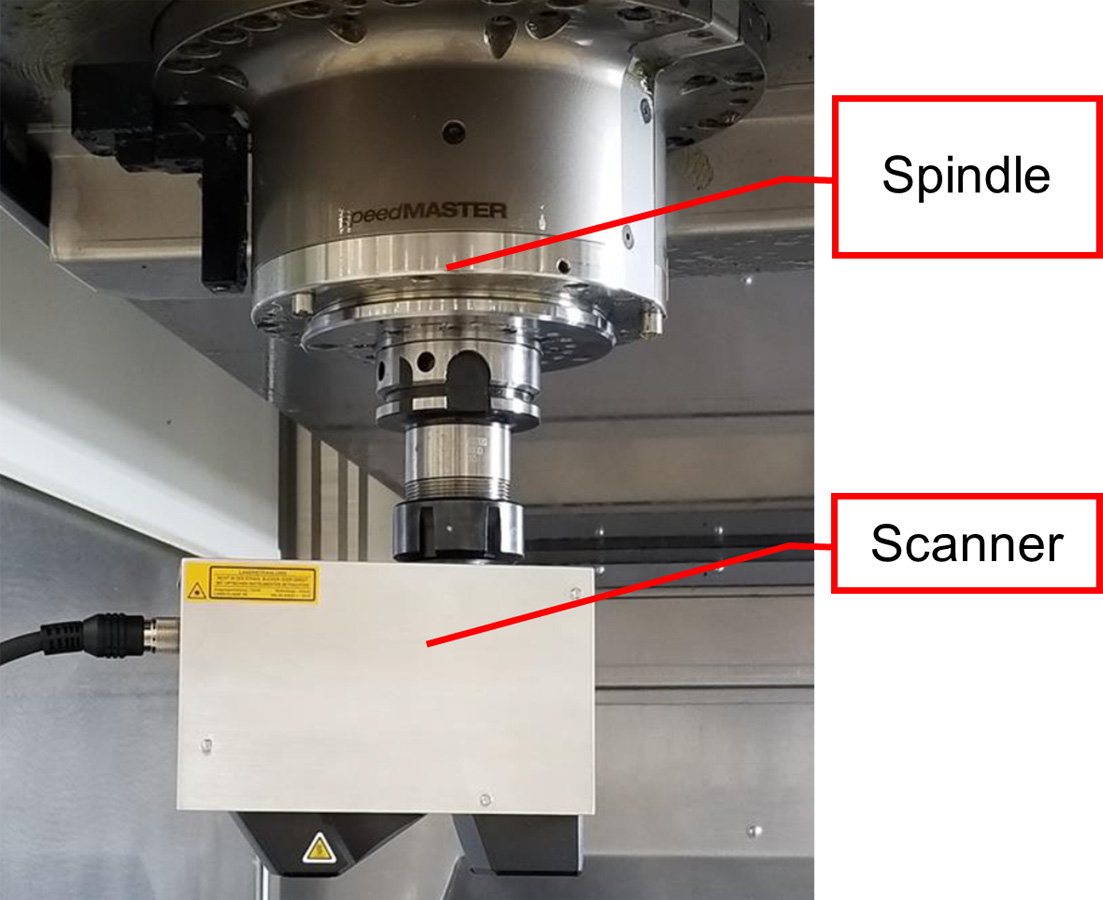
ES3 integrated a Keyence 3D scanner to the DMG Hybrid machine; this allows for pre-repair inspection, deposition repair, machining, and post-repair inspection all in one machine setup.
ES3 also develops Extreme High-Speed Laser Application (EHLA) DED processes. The EHLA process has advantages over traditional DED including 1) up to 3X deposition speed, 2) up to 10x smaller heat affected zone, 3) reduces energy and material waste (up to 95% material efficiency), 4) up to 10x thinner layers for precise coatings, 5) better surface finish. For example, ES3 developed a tungsten carbide wear coating process for gas turbine engine parts of Incoloy 901 and 4340 Steel substrates. The developed system is a hybrid which both DED deposits material and performs subtractive machining.
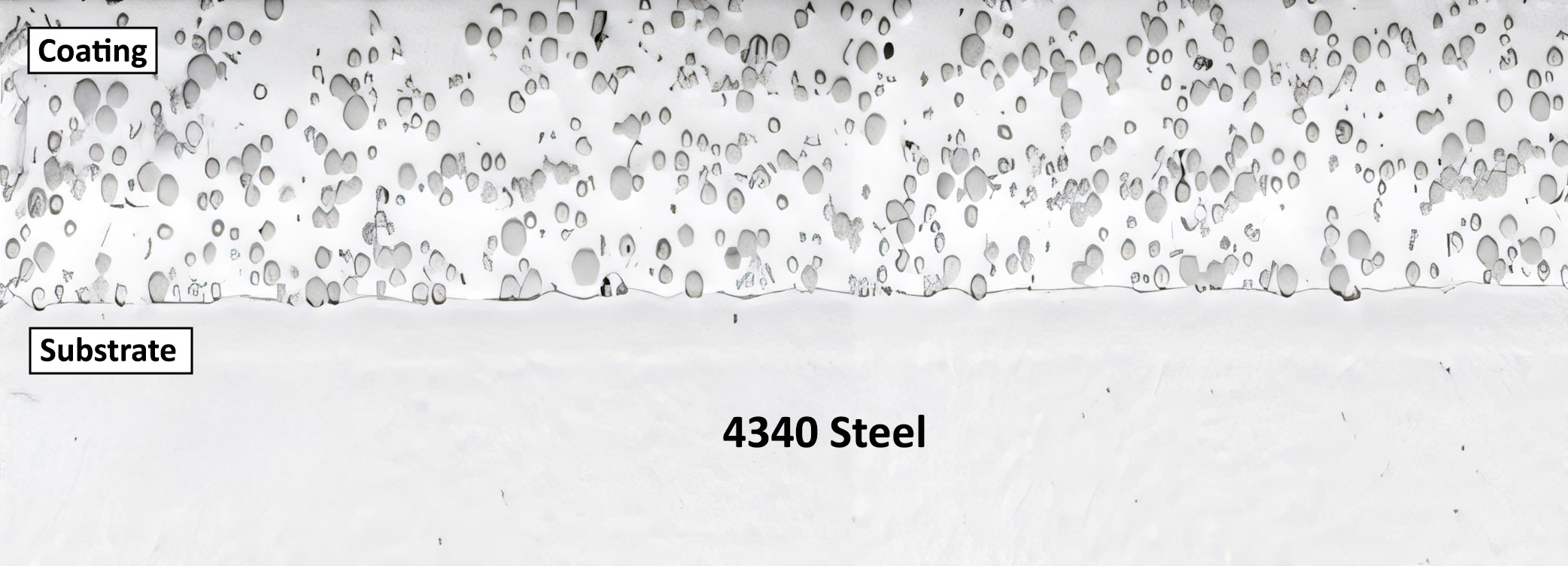
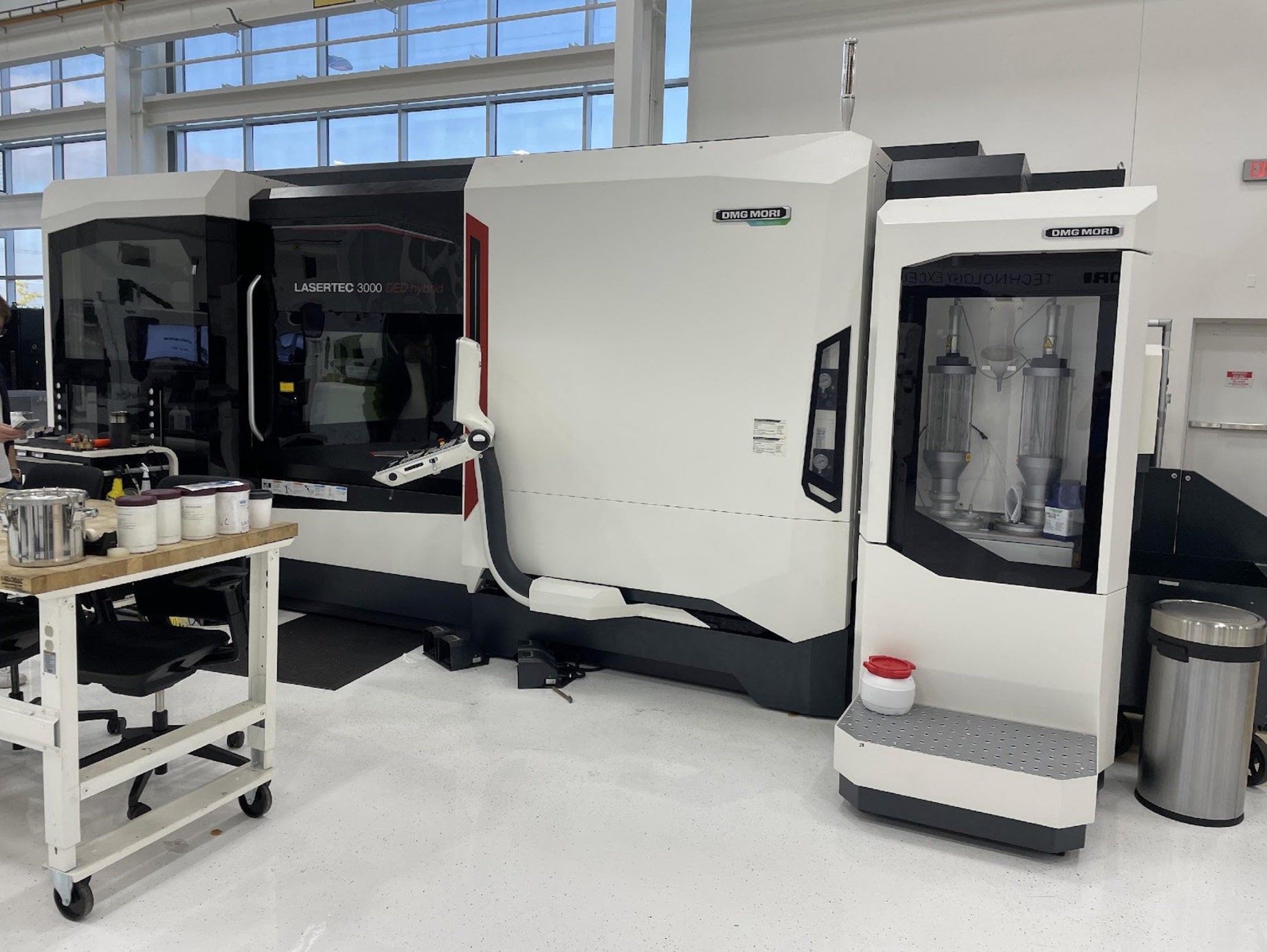
EBAM
ES3 has utilized both the Electron Beam Additive Manufacturing (EBAM) & Laser Powder Bed Fusion (LPBF) DED process to provide USAF AM alternatives to costly and time-consuming forging for critical landing gear components. ES3 developed optimized processing parameters, completed tensile and fatigue testing of AM materials, and performed full scale limit load testing of an AM Version of a B-1 MLG Positioner Fitting Assembly. The ES3 AM B-1 Positioner Fitting passed the prescribed limit load testing without failure. EBAM was used to fabricate the B-1 Positioner Fitting with 4340 HSS, while an EOS based LPBF process was used for the AMS 4640 Aluminum Nickel Bronze Bushings (AlNiBr).
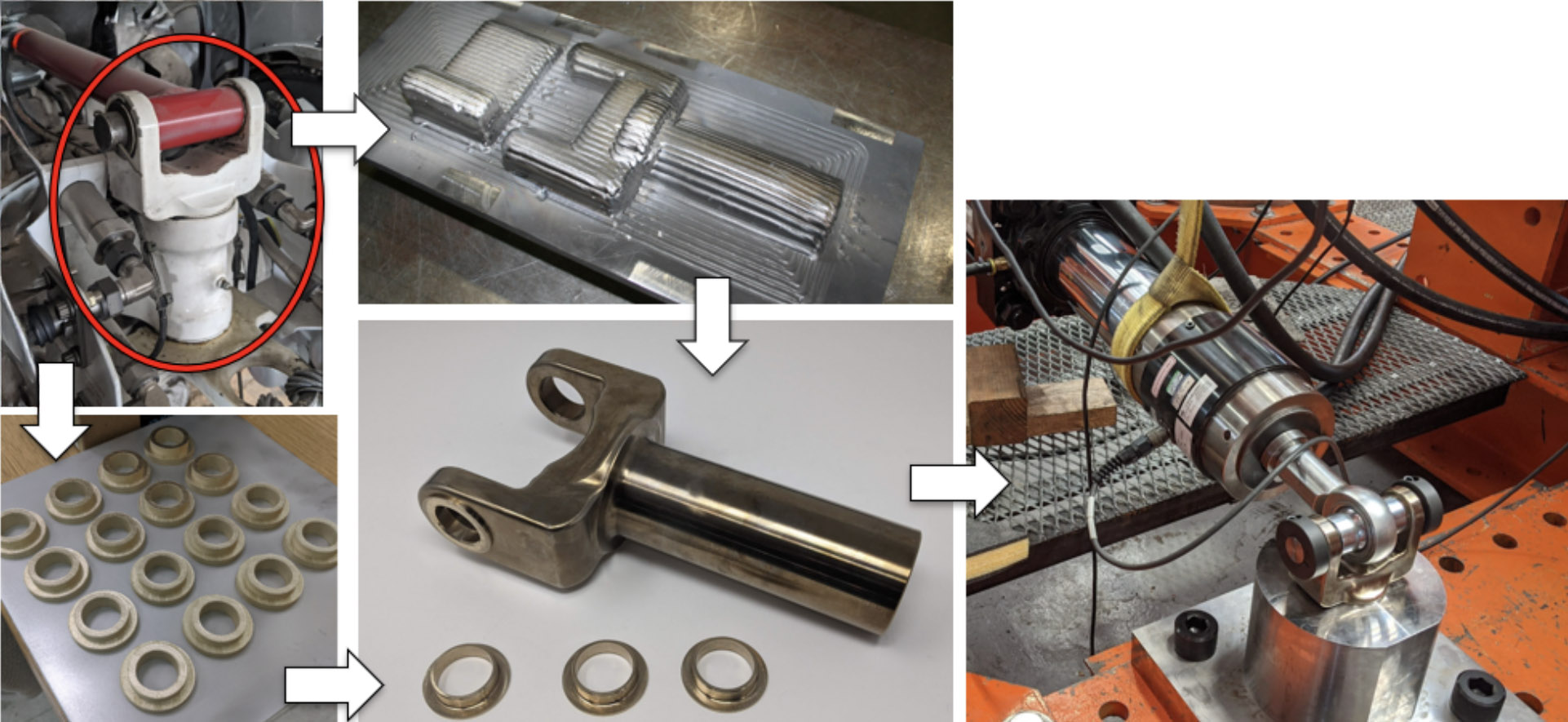